An ingenious way of providing safe access for pedestrians around the stockpiles and plant area at Hanson UK’s Needingworth sand and gravel quarry in Cambridgeshire has won a top industry award.
Health, safety and well being
Our safety performance in 2017 was mixed. The total number of lost time injuries (LTIs) remained static at 21, but a new record of 90 days without an LTI was set in May. The employee LTI frequency rate of injuries per one million hours worked, which has been adopted as a standard industry indicator, fell from 1.84 to 1.64.
The employee LTI severity rate, derived from the total number of days lost, rose slightly from 50.2 to 52.2.
We held safety stand-downs in May and October when the entire business came to a halt for two hours on a Monday morning. CEO Daniel Cooper introduced both sessions via a conference call and presentations on safety topics were delivered. The final hour was spent on a ‘hazard spot’ site tour, encouraging employees, contractors and drivers to identify and eliminate potential risks and look at ways to improve site services and welfare.
The May stand-down featured a short film made at Port Talbot Regen plant in south Wales, which was named as the UK’s best site in HeidelbergCement’s 2016 safe work - healthy lives competition.
The video showed how the Port Talbot team had developed a strong safety culture after a serious accident in 2008, and why good housekeeping is such an important element in eliminating accidents.
The October session, which was linked to Heidelberg Cement’s safety week, focused on drivers and introduced the forthcoming 2018 health and wellbeing programme.
This new initiative to improve health and wellbeing was formally launched in January 2018. It includes quarterly themed activities to support the campaign and a partnership with the charity Mates in Mind, which aims to raise awareness, address the stigma of poor mental health and improve positive mental wellbeing in the UK construction industry.
We will be working closely with Mates in Mind throughout 2018 to raise awareness of mental health issues as well as educating employees to recognise warning signs and offer appropriate support. The aim is to remove the stigma and encourage people to talk about problems they may be facing and work together to overcome them.
We engage with our work force through safety conversations and encouraging near-hit reporting, both of which increased during the year, along with regular tool box talks and best practice alerts. We also have regular one-to-one safety discussions with all employees along with comprehensive health and safety training from both in-house specialists and external consultants delivered through monthly conference calls, podcasts and on-site discussions supported by our sustainability representative network. We continue to deliver the Mineral Products Association’s ‘Safer by Competence’ programme.
Our round-the-clock telephone counselling service EmployeeCare provides confidential support on a broad range of work-related and personal issues from financial management and relationships to health, drugs and bereavement.
We continued with our programme of random and unannounced drugs and alcohol testing at operational sites and offices. The testing is combined with an awareness campaign to explain the impact and effects of different types of drugs and encourage employees who think they may be at risk to seek help and support.
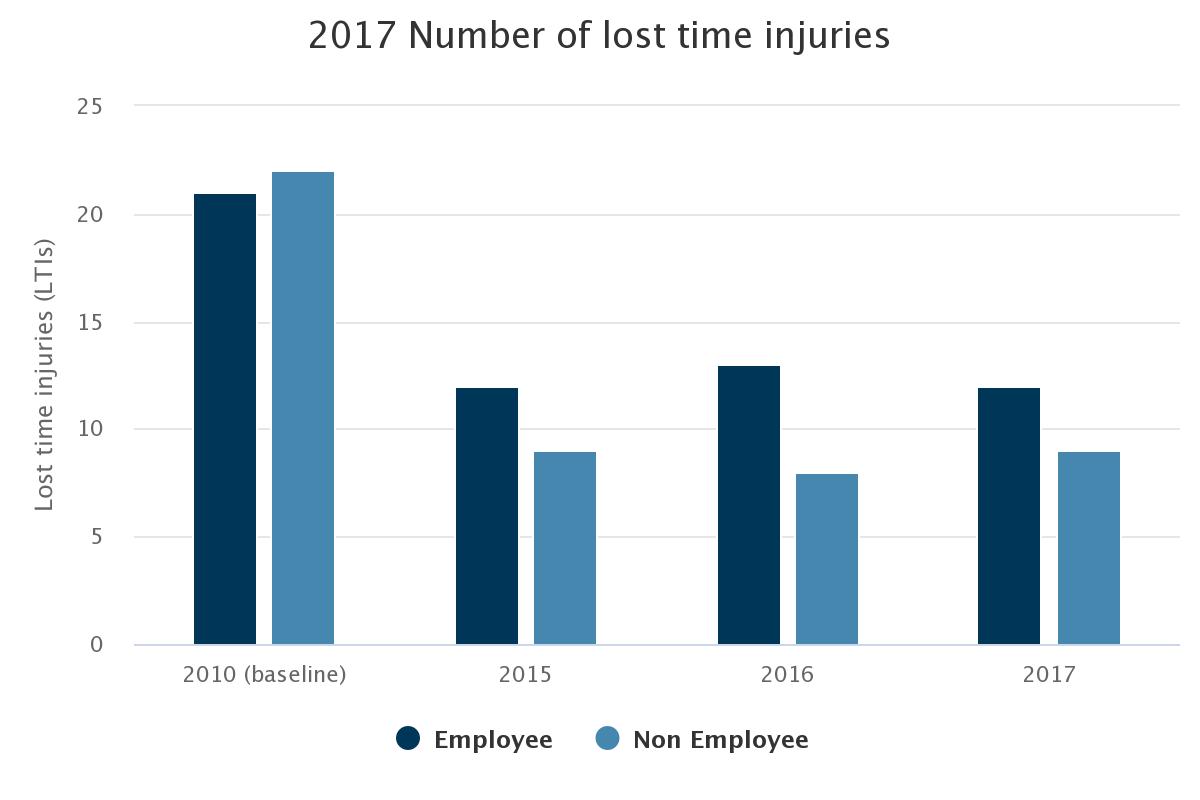
-
Lost time injuries data
Click here for data by business line2010 (baseline)
2015
2016
2017
Employees
21
12
13
12
Contractors
22
9
8
9
Employee severity rate
44.2
77.3
50.3
52.2
Employee frequency rate
2.66
1.74
1.84
1.64